Rooftop Fall Protection: Navigating Code vs. OSHA Compliance
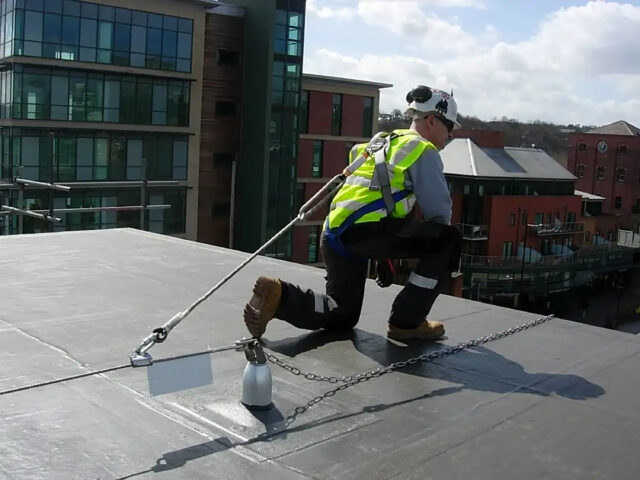
“Make sure the equipment is 10 feet from the roof edge, so you don’t need guards per Code.” This editor’s note on a recent mechanical roof plan seems simple enough—meet the Code and move on. The Code in this case is the 2020 Mechanical Code of NY State, which is based on the 2018 International Building Code. Specifically, Section 304.11 Guards defines requirements for guards, including their height, opening limitations, and where they must be placed in relation to the equipment.
The U.S. Occupational Safety and Health Administration (OSHA) also provides safety guidelines for workers. For many years, OSHA’s fall protection requirements paralleled those in the Code, making compliance fairly simple—if your building met the Code, it likely met OSHA’s guidelines as well. However, significant changes to OSHA regulations took effect in January 2017, expanding fall protection requirements and acceptable options to provide it. This deviates from the Code’s “10-foot rule,” making it critical to understand the differences between the Code and OSHA regulations for effective safety management.
OSHA Standards for Fall Protection
OSHA establishes safety and health regulations for construction under OSHA Standard 1926 Subpart M, as well as for “general industry” under OSHA Standard 1910, which applies to building owners and their employees carrying out general operation and maintenance tasks after construction is complete. As a building owner or operator, collaborating with your design team can help you choose the compliance method that is best for you. If your chosen option requires architectural or structural elements, these can be incorporated into the design.
Fall Protection Options for Low-Slope Roofs
This discussion will focus on low-slope roofs, governed by OSHA Standard 1910 Subpart D—Walking-Working Surfaces, as they are the most common condition we encounter. OSHA 1910.28 outlines the employer’s duty to have fall protection and falling object protection. Specifically, employers must ensure that each employee on a walking-working surface with an unprotected side or edge at least 4 feet or more above a lower level is protected from falling using one of several methods.
While the best way to prevent falls is to keep workers off the roof, placing large equipment inside a building can be cost-prohibitive. This option often requires considerable space and necessitates exterior connections for combustion, supply, and exhaust air, which can be challenging in existing structures and complicate future expansions.
When equipment is placed on the roof, fall protection methods vary depending on the distance to the edge. It is important to note that while the Code sets distances for equipment, OSHA focuses on the employee’s position relative to the edge. Current regulations categorize protection levels into three zones: less than 6 feet from the roof edge, between 6 and 15 feet from the edge, and greater than 15 feet from the edge.
Less Than 6 Feet From the Roof Edge
Per OSHA 1910.28(b)(13)(i), when work is performed less than 6 feet from the roof edge, the employer must ensure each employee is protected from falling using a guardrail system, safety net system, travel restraint system, or personal fall arrest system.
Guardrail System: A guardrail system can be permanent or free-standing, as long as it meets the criteria set forth in OSHA 1910.29(b). Guardrails are a straightforward solution, as they offer protection in all zones and are passive, requiring no special training or actions from employees. However, a full guardrail system can be costly, unsightly, and may lead to additional penetrations in the roof system.
Safety Net System: A safety net system is installed below a roof edge to catch personnel after they have fallen. Typically used in construction activities or industrial applications where other options are limited (see OSHA 1926.502(c), these systems are an acceptable form of employee protection. They require regular maintenance and drop-testing and have a more limited lifespan.
Travel Restraint System: Per OSHA 1910.140, a travel restraint system consists of an anchorage, anchorage connector, lanyard (or other means of connection), and body support, designed to prevent an employee from reaching the edge of a walking-working surface. As designers, we delegate system’s engineering to the manufacturer while specifying connection details at the anchorage points. As owners, you are responsible for providing personal protective equipment, training staff on its use, and enforcing compliance.
Personal Fall Arrest System: This system is used to arrest an employee in a fall from a working level. It includes an anchorage, connectors, and a body harness, and may also incorporate a lanyard, deceleration device, lifeline, or suitable combinations of these. Like travel restraint systems, this option requires you to provide personal protective equipment, staff training, and compliance enforcement. Proper anchor point placement is critical, as the employee’s equipment is calibrated based on the distance from anchor to roof edge, as well as its height. The design and detailing of anchor points are also crucial, as they often penetrate the roof system and connect to structural elements. (See OSHA 1926.502(d).)
6 to 15 Feet From the Roof Edge
Per OSHA 1910.28(b)(13)(ii), when work is performed between 6 feet and 15 feet from the roof edge, the employer must ensure each employee is protected from falling by guardrails, safety nets, travel restraints, or personal fall arrest systems. The employer may use a designated area, defined in OSHA 1910.29(d), when performing work that is both infrequent and temporary. This area is physically indicated on the rooftop by a “warning line” (e.g., rope, wire, tape, or chain) and is typically adorned with flags for visibility. A designated area can be either permanent or temporary, requiring setup each time rooftop work is scheduled.
15 Feet or More From the Roof Edge
Per OSHA 1910.28(b)(13)(iii), when work is performed 15 feet or more from the roof edge, the employer must protect employees from falling by using guardrails, safety nets, travel restraints, personal fall arrest systems, or a designated area. However, the employer is not required to provide any fall protection if the work is both infrequent and temporary, and they implement and enforce a work rule that prohibits employees from coming within 15 feet of the roof edge.
This is the least restrictive option, provided equipment is placed at least 18 feet from the roof edge, allowing for a 3-foot work zone around the equipment while maintaining the 15-foot setback. A designated area can be marked on the roof surface with a permanent stripe in a contrasting color. Many single-ply roof membrane manufacturers offer products for this purpose.
Special Considerations
In addition to roof edges, the same safety measures are required around “holes,” such as skylights installed before fall protection was required by Code and open roof hatches. Most hatch manufacturers have an OSHA-compliant railing system that can be specified as an accessory.
Ensuring OSHA Compliance in Building Design
In summary, while the Code provides essential guidelines for equipment placement on rooftops, it is crucial to recognize that OSHA regulations impose additional and sometimes more stringent fall protection requirements. This shift from the traditional “10-foot rule” underscores the importance of proactive safety management in rooftop environments.
Building owners and operators must not only adhere to the Code but also ensure compliance with OSHA standards to effectively safeguard employees. Since the Building Code does not prescribe OSHA measures, the responsibility for compliance lies with the building owner or operator.
As designers, we can assist you in understanding the interplay between the Code and OSHA compliance, helping you select the best option—or combination of options—to protect your employees and meet OSHA standards.

About the Author
Scott R. Perry, AIASenior Project Manager
Scott is an accomplished architect and project manager with 30 years of experience at multiple award-winning firms. Specializing in K-12 educational facilities, he has a proven track record of successful projects. His expertise includes identifying opportunities, quality management, meticulous attention to detail, and extensive construction knowledge.